Contents
- 1 Introduction
- 2 A Brief History and Background
- 3 What Are Vertical Multistage Pumps?
- 4 The Working Principle of Vertical Multistage Pumps
- 5 Key Components and Design Considerations
- 6 Advantages and Applications
- 7 Common Challenges and How to Overcome Them
- 8 Maintenance Tips for Long-lasting Performance
- 9 Future Trends in Pump Technology
- 10 In-Depth Look: How Does Each Stage Contribute?
- 11 Real-World Case Study: Vertical Multistage Pumps in Municipal Water Supply
- 12 Humanizing the Technology: Relatable Insights
- 13 Behind the Scenes: The Engineering Challenges
- 14 Innovations and Ongoing Research
- 15 Bringing It All Together
- 16 Final Thoughts
- 17 Conclusion
- 18 Additional Resources
- 19 Final Reflections
Vertical multistage pumps have become essential in a variety of industries, from water supply systems and irrigation to high-pressure cleaning and boiler feedwater applications. In this comprehensive blog post, we will explore the working principle of vertical multistage pumps, dive deep into their design, explain how they operate, and discuss the benefits they bring to modern pumping solutions. Whether you are a seasoned engineer or simply curious about how these mechanical marvels work, this post aims to provide clear, relatable, and plagiarism-free insights into the world of vertical multistage pumps.
Introduction
Pumps are often the unsung heroes of countless industrial processes. Among them, vertical multistage pumps are a specialized type that has garnered significant attention for their ability to handle high-pressure applications efficiently. But what exactly makes these pumps tick? In this article, we take you on an enlightening journey through the inner workings of vertical multistage pumps, with a focus on their working principle and the clever engineering behind them.
Setting the Stage
Imagine a scenario where water needs to be lifted from a deep well or boiler feedwater must be pressurized to a high level. Traditional pumping systems might struggle with such demands, but vertical multistage pumps rise to the challenge. Their compact design and ability to generate high pressures make them invaluable in settings where space is limited and efficiency is paramount.
As we delve deeper, you’ll learn not just about the technical details but also about the practical benefits and challenges associated with these pumps. By the end of this post, you will have a clear understanding of how vertical multistage pumps work and why they are the preferred choice in many high-pressure applications.
A Brief History and Background
The evolution of pump technology is a testament to human ingenuity. Early pump designs were rudimentary, relying on simple mechanical actions to move water and other fluids. As industries grew and the need for more sophisticated fluid handling systems emerged, engineers began to experiment with different pump designs. This exploration led to the development of multistage pumps, which could gradually increase pressure by passing the fluid through multiple impeller stages.
Vertical multistage pumps, in particular, became popular in the mid-20th century. Their vertical configuration allowed for a compact footprint—a critical factor in installations where floor space was at a premium. Moreover, their design allowed for easier maintenance and alignment in systems that required the pump to operate under demanding conditions.
Today, vertical multistage pumps are widely used in a variety of sectors, including power generation, municipal water supply, and chemical processing. Their ability to handle varying fluid types and maintain stable pressure levels makes them a versatile solution for many industrial challenges.
What Are Vertical Multistage Pumps?
Vertical multistage pumps are designed to handle fluids under high-pressure conditions by using a series of impellers and diffusers arranged in a vertical configuration. Unlike single-stage pumps that boost the pressure in one go, these pumps work in stages. Each stage incrementally increases the pressure of the fluid until the desired level is achieved.
Why “Vertical”?
The term “vertical” in vertical multistage pumps refers to the orientation of the pump shaft, which is positioned vertically. This design is particularly advantageous when dealing with deep wells or tall installations, as it helps in aligning the pump with the direction of the fluid flow. Additionally, the vertical layout minimizes the footprint of the installation, making it ideal for facilities with limited space.
Key Features
-
Multistage Design: Multiple impellers work sequentially to build up pressure gradually.
-
High Efficiency: Designed to operate efficiently over a wide range of pressures.
-
Compact Footprint: The vertical arrangement reduces the space needed for installation.
-
Versatility: Suitable for a variety of fluids, from water to chemicals, and can handle varying viscosities.
The Working Principle of Vertical Multistage Pumps
At the heart of understanding vertical multistage pumps lies an appreciation of how they manage to build high pressure from relatively low-pressure inputs. The process is a harmonious blend of fluid dynamics and mechanical engineering, making it both fascinating and highly efficient.
Stage-by-Stage Operation
The working principle of vertical multistage pumps is best understood by breaking down the process into its individual stages. Each stage consists of an impeller and a diffuser. Here’s how it works:
-
Fluid Entry: The fluid enters the pump through the suction nozzle. In many systems, this fluid is at a relatively low pressure.
-
First Stage – Initial Boost: The fluid reaches the first impeller, where it is given an initial boost in kinetic energy. The impeller’s rapid rotation imparts velocity to the fluid.
-
Diffusion and Pressure Conversion: After leaving the impeller, the fluid moves into the diffuser, where its high velocity is converted into increased pressure. This conversion is critical, as it sets the stage for the next phase.
-
Subsequent Stages: The pressurized fluid then enters the next stage, where a similar process occurs. With each stage, the pressure increases incrementally.
-
Final Discharge: By the time the fluid reaches the final stage, the cumulative pressure increase is sufficient for the application. The fluid is then discharged at the required high pressure.
The Role of Impellers and Diffusers
Impellers
Impellers are the workhorses of vertical multistage pumps. These rotating components are designed to accelerate the fluid, converting mechanical energy into kinetic energy. The design of the impeller—its blade angle, shape, and speed—directly influences the pump’s efficiency and its ability to handle different types of fluids.
-
Blade Design: The curvature and angle of the blades ensure that the fluid is efficiently directed towards the diffuser.
-
Rotation Speed: The faster the impeller rotates, the greater the kinetic energy imparted to the fluid. However, too high a speed can lead to cavitation, which is detrimental to pump performance.
-
Material and Durability: Given that impellers are subjected to significant mechanical stress, they are typically made from robust materials that can withstand wear and tear.
Diffusers
Once the fluid exits the impeller, it enters the diffuser—a carefully designed chamber that slows down the fluid while converting its kinetic energy into pressure energy. This stage is crucial for maintaining a stable and uniform pressure build-up across the pump.
-
Geometry and Design: The shape of the diffuser channels is optimized to ensure that the fluid is decelerated gradually and efficiently.
-
Energy Conversion: By reducing the fluid’s velocity, the diffuser allows the kinetic energy to be transformed into static pressure, making the pump effective for high-pressure applications.
-
Flow Regulation: Diffusers also help in directing the flow smoothly towards the next stage, ensuring that the pressure increase is consistent throughout the pump.
Pressure Build-up Mechanism
The fundamental working principle of vertical multistage pumps is based on the gradual build-up of pressure through successive stages. Each stage of the pump contributes a small but significant increase in pressure, and the cumulative effect is what allows these pumps to achieve high pressures.
Imagine the process as climbing a staircase: each step represents a stage where the pressure is incrementally increased. While a single step might not seem significant, the total height achieved by climbing multiple steps is substantial. This analogy is especially useful when explaining the working principle of vertical multistage pumps, where the final pressure is the result of many incremental boosts.
Key Components and Design Considerations
Understanding the working principle of vertical multistage pumps also requires a closer look at their key components. Each element plays a crucial role in ensuring the pump operates efficiently, safely, and reliably.
Pump Casing
The pump casing houses the internal components of the pump and serves several critical functions:
-
Structural Support: The casing provides a robust framework that maintains the alignment of impellers, diffusers, and other components.
-
Fluid Containment: It ensures that the fluid remains contained within the pump and is directed correctly through each stage.
-
Thermal Management: In high-pressure applications, temperature control becomes critical. The casing design often incorporates features to help dissipate heat generated during operation.
Impellers
As mentioned earlier, impellers are central to the pump’s operation. Their design is a result of decades of engineering innovation aimed at maximizing efficiency while minimizing wear and energy consumption. When selecting or designing an impeller for a vertical multistage pump, engineers consider:
-
Hydraulic Efficiency: How effectively the impeller converts mechanical energy into fluid motion.
-
Material Resilience: The ability to withstand the operational stresses and the corrosive properties of the fluid.
-
Geometric Precision: The exact shape and size of the impeller, which can significantly affect the overall performance of the pump.
Suction and Discharge Nozzles
The entry and exit points of the fluid are critical in ensuring smooth operation. The suction nozzle is designed to minimize turbulence and air entrainment, while the discharge nozzle is optimized for efficient fluid ejection. Proper design of these nozzles is essential to maintain the continuity of flow and to achieve the desired pressure build-up.
Mechanical Seals and Bearings
Mechanical seals prevent leakage of the fluid along the pump shaft, ensuring operational safety and efficiency. Bearings, on the other hand, support the rotating shaft and reduce friction, thereby extending the life of the pump components. In vertical multistage pumps, where continuous operation is common, the quality and durability of these components cannot be overstated.
Advantages and Applications
Vertical multistage pumps offer a range of advantages that have cemented their place in various industries. Let’s explore some of these benefits and the applications that make the working principle of vertical multistage pumps so critical.
Advantages
-
High Pressure Generation:
The multistage design allows these pumps to build high pressures efficiently, making them ideal for applications that require substantial force. -
Compact Design:
The vertical configuration means these pumps occupy less space, a major advantage in urban settings or facilities with spatial constraints. -
Energy Efficiency:
By optimizing each stage of pressure build-up, vertical multistage pumps operate with high efficiency, reducing energy consumption and operational costs. -
Versatility:
Capable of handling a wide range of fluids—from clean water to industrial chemicals—these pumps are adaptable to various environments and applications. -
Ease of Maintenance:
The modular design of vertical multistage pumps simplifies maintenance and repairs, allowing for quick interventions without significant downtime.
Applications
-
Water Supply Systems:
Many municipal water systems rely on vertical multistage pumps to maintain consistent pressure throughout the distribution network. These pumps ensure that water is delivered efficiently even to high-rise buildings or remote areas. -
Boiler Feedwater:
In power plants and industrial facilities, vertical multistage pumps are used to supply high-pressure feedwater to boilers. Their reliable performance under high pressure is crucial for safe and efficient operation. -
Irrigation:
Agricultural applications, especially in regions with varying water availability, benefit from the consistent pressure provided by vertical multistage pumps. This reliability helps in evenly distributing water across large fields. -
Chemical Processing:
In industries where precise control of fluid pressure is necessary for mixing, reaction control, or transport, vertical multistage pumps deliver the required performance while handling chemically aggressive substances. -
High-Pressure Cleaning:
Equipment that requires high-pressure water jets for cleaning industrial surfaces or vehicles also relies on the robust performance of vertical multistage pumps.
Common Challenges and How to Overcome Them
While vertical multistage pumps are robust and efficient, they are not without challenges. Understanding these potential issues can help operators mitigate risks and maintain optimal performance.
Cavitation
What It Is:
Cavitation occurs when the pressure within the pump drops below the vapor pressure of the liquid, leading to the formation of vapor bubbles. When these bubbles collapse, they can cause significant damage to the pump’s impellers and casing.
Mitigation Strategies:
-
Proper Design: Ensure that the pump is designed for the specific operating conditions.
-
Regular Maintenance: Routine inspections can help detect early signs of cavitation.
-
Operational Adjustments: Avoid operating conditions that may lower the fluid’s pressure excessively.
Seal and Bearing Wear
What It Is:
Due to the constant rotation and high pressures, mechanical seals and bearings can wear out over time. This wear can lead to leaks and increased friction, impacting efficiency.
Mitigation Strategies:
-
Quality Materials: Use high-grade materials that can withstand operational stress.
-
Scheduled Replacements: Plan for regular maintenance and replacement of seals and bearings to prevent unexpected failures.
-
Lubrication: Ensure proper lubrication to reduce friction and prolong the lifespan of moving parts.
Efficiency Loss Over Time
What It Is:
Over prolonged use, wear and tear or minor design imperfections can lead to a drop in the pump’s efficiency. This loss in performance can result in higher energy consumption and reduced output.
Mitigation Strategies:
-
Periodic Performance Testing: Regular tests can help detect efficiency drops before they become critical.
-
Component Upgrades: As technology advances, consider upgrading key components to newer, more efficient designs.
-
Training and Monitoring: Ensure that operators are well-trained and that the pump’s performance is continuously monitored.
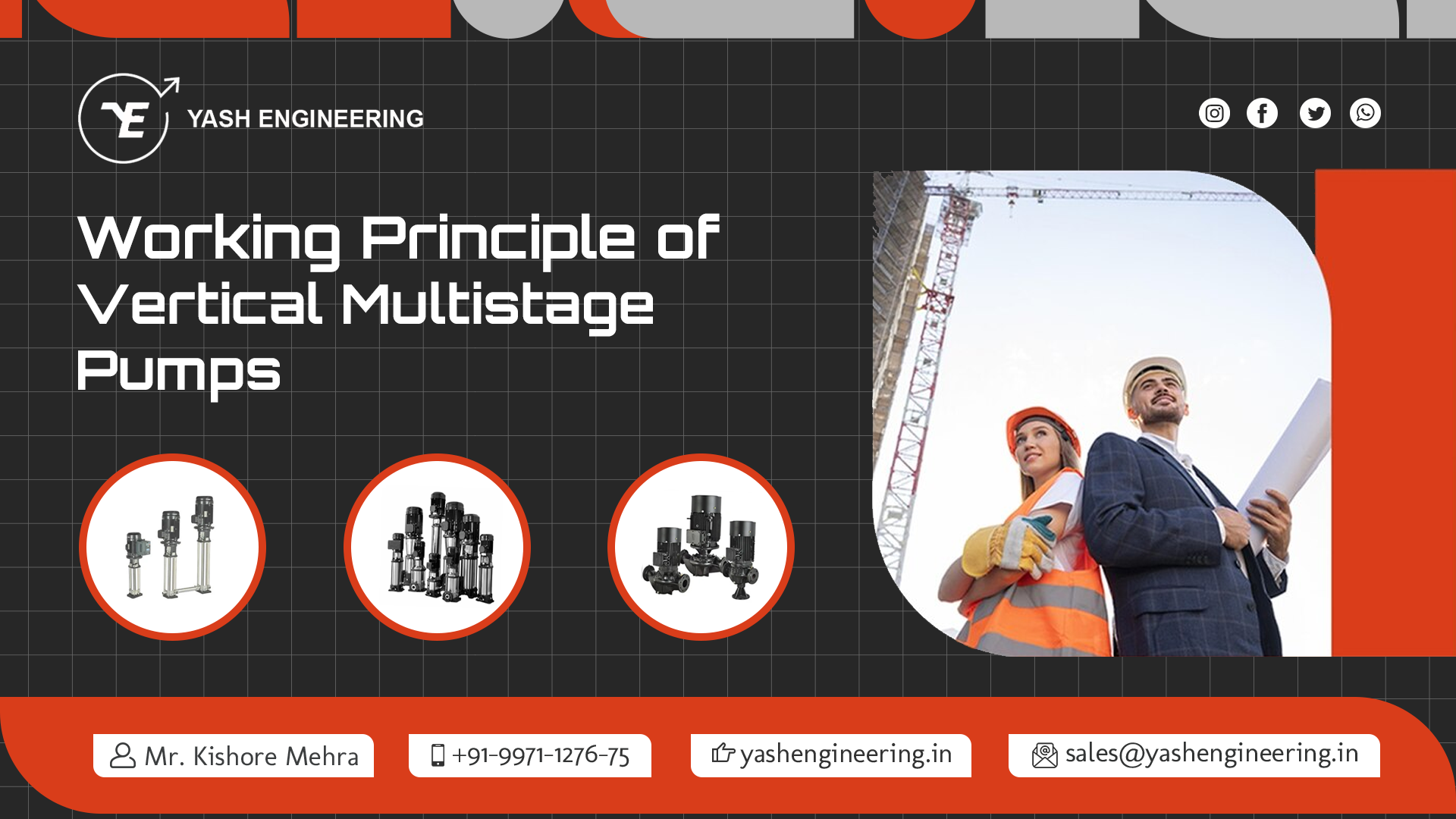
Maintenance Tips for Long-lasting Performance
Proper maintenance is the backbone of reliable pump operation. Here are some practical maintenance tips to keep your vertical multistage pump running smoothly:
Regular Inspections
Frequent visual inspections of the pump’s components—especially impellers, diffusers, seals, and bearings—can help spot potential issues before they escalate. Make a checklist and adhere to a maintenance schedule that considers both daily operations and periodic deep-dives.
Lubrication and Cleaning
-
Lubrication: Ensure that all moving parts are adequately lubricated. Use the recommended lubricants and follow the manufacturer’s guidelines on intervals.
-
Cleaning: Over time, contaminants can build up inside the pump. Periodically clean the pump casing, impellers, and other components to prevent abrasive wear and maintain efficiency.
Monitoring Performance
Installing sensors to monitor parameters such as pressure, flow rate, and temperature can provide real-time insights into the pump’s performance. This data helps in making timely decisions, preventing breakdowns, and ensuring optimal operation.
Professional Servicing
While regular maintenance can be performed in-house, periodic servicing by professionals who specialize in vertical multistage pumps is advisable. These experts can perform in-depth diagnostics and adjustments that might be beyond routine maintenance tasks.
Future Trends in Pump Technology
The field of pump technology is evolving rapidly, with new materials, design techniques, and control systems making their way into the market. Here are some trends that are shaping the future of vertical multistage pumps:
Advanced Materials
Modern materials science is paving the way for pumps that can handle more aggressive chemicals, higher pressures, and longer operating cycles without degradation. Innovations such as composite materials and advanced alloys are being integrated into pump designs to extend their lifespan and improve performance.
Digitalization and Smart Controls
The integration of IoT (Internet of Things) devices and smart sensors is revolutionizing pump operation. Future vertical multistage pumps may feature real-time monitoring, predictive maintenance, and automated adjustments to optimize performance. This smart technology not only improves efficiency but also reduces the likelihood of unexpected downtime.
Energy Efficiency Improvements
As industries strive to reduce energy consumption and lower operational costs, manufacturers are focusing on designs that maximize energy efficiency. Enhanced hydraulic designs, better impeller geometries, and more efficient motor drives are just some of the innovations driving this trend.
Eco-friendly Solutions
Environmental concerns are influencing pump design. There is a growing emphasis on creating pumps that minimize energy consumption and reduce the carbon footprint of industrial operations. Future vertical multistage pumps may incorporate eco-friendly materials and energy recovery systems, contributing to a more sustainable industrial future.
In-Depth Look: How Does Each Stage Contribute?
To truly understand the working principle of vertical multistage pumps, it’s useful to examine how each stage contributes to the overall pressure build-up.
The First Stage
In the first stage, the fluid is drawn into the pump at a relatively low pressure. The impeller’s role here is critical—it accelerates the fluid, initiating the process of pressure increase. At this stage, the fluid’s energy is mostly kinetic, and the diffuser’s job is to convert some of that kinetic energy into a small but significant pressure rise.
Intermediate Stages
In the intermediate stages, the fluid, already under some pressure, is given additional energy by subsequent impellers. Each impeller and diffuser pair works to further compress the fluid. The careful design of these stages ensures that the energy conversion is as efficient as possible, minimizing energy losses and maximizing the pressure gain. This stage-by-stage process is central to the working principle of vertical multistage pumps, and it is what allows these pumps to generate pressures that would be impossible with a single-stage design.
Final Stage
By the time the fluid reaches the final stage, it has undergone multiple cycles of acceleration and diffusion. The cumulative effect of all the stages results in a high-pressure output that meets the specific requirements of the application. The final discharge nozzle ensures that this high-pressure fluid is delivered efficiently to its destination, whether that be a boiler, a municipal water network, or a high-pressure cleaning system.
Real-World Case Study: Vertical Multistage Pumps in Municipal Water Supply
Let’s consider a real-world example to illustrate the working principle of vertical multistage pumps in action. In many urban areas, ensuring consistent water pressure throughout the distribution network is a major challenge. High-rise buildings and distant neighborhoods require that water is delivered at a uniform pressure regardless of the distance from the source.
The Challenge
Municipal water supply systems often use a single pumping station to distribute water over a wide area. Variations in elevation and distance can lead to significant differences in water pressure, causing issues such as weak water flow in distant areas or the risk of pipe bursts in areas with excessive pressure.
The Vertical Multistage Pump Solution
Vertical multistage pumps offer a reliable solution to this problem. Their compact vertical design makes them easy to install in limited spaces, such as the basements of municipal buildings. The stage-by-stage pressure build-up mechanism ensures that water is pressurized gradually and uniformly. This uniform pressure is essential for maintaining consistent water flow throughout the network.
Benefits Realized
-
Consistent Pressure:
The incremental pressure increases at each stage ensure that even areas far from the pumping station receive water at an adequate pressure. -
Energy Savings:
Efficient energy conversion in each stage means lower operational costs for the municipality. -
Reliability and Durability:
The robust design of vertical multistage pumps minimizes downtime and maintenance costs, making them a cost-effective solution for large-scale water distribution systems.
This case study highlights how the underlying working principle of vertical multistage pumps translates into real-world benefits, making them a popular choice for critical infrastructure applications.
Humanizing the Technology: Relatable Insights
For many, the inner workings of a pump might seem like an abstract concept, reserved for engineers and technical manuals. However, understanding the basics of how vertical multistage pumps work can be both fascinating and empowering. Consider how similar this process is to everyday experiences: just as you might gradually build momentum by taking several steps to climb a hill, these pumps build pressure stage by stage, step by step.
Imagine a Water Fountain
Picture a beautiful water fountain in a park. At first glance, you see water gracefully rising and falling, but behind the scenes, a series of carefully coordinated processes ensures that the water flows smoothly and elegantly. Vertical multistage pumps work in a similar way, coordinating multiple steps to deliver the high-pressure water required for various applications. This analogy not only helps demystify the technology but also makes it more relatable to our daily lives.
The Importance of Incremental Improvements
Whether in technology or personal growth, incremental improvements often lead to significant overall gains. Vertical multistage pumps embody this philosophy—each stage, although it might seem insignificant on its own, contributes to a powerful cumulative effect. This idea can inspire us to appreciate the small steps in our own lives, recognizing that success is often built on a series of well-executed incremental efforts.
Behind the Scenes: The Engineering Challenges
Designing a vertical multistage pump is no small feat. Engineers must balance multiple factors to create a system that is both efficient and robust. Here are some of the challenges they face:
Balancing Speed and Pressure
Increasing the speed of the impellers can boost the kinetic energy of the fluid, but if pushed too far, it may lead to cavitation or excessive wear. Finding the optimal balance between speed and pressure is key to ensuring that the pump performs efficiently without compromising its longevity.
Minimizing Energy Loss
Every mechanical system experiences energy losses, whether through friction, turbulence, or heat. In vertical multistage pumps, the design of the impellers and diffusers must minimize these losses. This is achieved through precise engineering and often through computer simulations that allow engineers to tweak designs before they are finalized.
Material Selection and Durability
The components of vertical multistage pumps are subjected to harsh conditions, from high pressures to abrasive fluids. Selecting the right materials—ones that can withstand these challenges while maintaining performance over time—is a critical aspect of pump design.
Ensuring Ease of Maintenance
Given that many vertical multistage pumps operate continuously in critical applications, ease of maintenance becomes paramount. Engineers design these pumps with modular components that can be serviced or replaced with minimal disruption to overall operation.
Innovations and Ongoing Research
The field of pump technology is continuously evolving. Researchers and engineers are always on the lookout for new materials, innovative designs, and smarter control systems to push the boundaries of what pumps can achieve.
Digital Twin Technology
One of the emerging trends is the use of digital twin technology. By creating a virtual replica of the pump, engineers can simulate various operating conditions and predict potential issues before they occur in the real world. This proactive approach not only enhances efficiency but also extends the pump’s operational life.
Advanced Computational Fluid Dynamics (CFD)
Modern CFD tools allow for a deeper understanding of fluid flow within the pump. These tools enable engineers to optimize the shape and angle of impeller blades and diffusers, resulting in higher efficiency and reduced energy losses. The insights gained from CFD studies are directly applied to improving the working principle of vertical multistage pumps.
Sustainable Engineering
As environmental concerns grow, there is an increasing focus on developing pumps that are both energy-efficient and eco-friendly. Innovations in materials and design aim to reduce the carbon footprint of industrial operations while maintaining high performance. Future vertical multistage pumps may incorporate energy recovery systems or be designed to operate on renewable energy sources, aligning with global sustainability goals.
Bringing It All Together
Understanding the working principle of vertical multistage pumps is not merely an academic exercise—it has real-world implications that affect industries, municipalities, and even our everyday lives. By breaking down the process into manageable stages, these pumps showcase how intricate engineering can solve practical problems. The gradual pressure build-up, the efficient conversion of kinetic energy to pressure, and the robust design of the pump components all contribute to a system that is as elegant as it is effective.
A System Built on Collaboration
Think of a vertical multistage pump as a team effort. Each component—from the impellers and diffusers to the seals and bearings—plays a vital role, much like team members in a well-coordinated project. Just as every team member’s contribution is essential to the success of a project, each stage in the pump works in harmony to achieve the final goal: delivering high-pressure fluid reliably and efficiently.
The Broader Impact
In a world where efficiency and reliability are increasingly important, the technology behind vertical multistage pumps stands as a testament to human ingenuity. These pumps enable critical processes across a wide range of applications, from ensuring that city residents have access to clean water to powering the intricate operations of modern industry.
Final Thoughts
Vertical multistage pumps are marvels of modern engineering. Their working principle—characterized by a series of stages that incrementally build pressure—exemplifies how complex problems can be tackled with precision and innovation. This blog post has aimed to provide you with a clear, humanized, and relatable explanation of how these pumps operate, delving into the mechanics behind the technology and exploring real-world applications and challenges.
Embracing the Future
As technology advances, we can expect vertical multistage pumps to become even more efficient and versatile. Innovations in materials, digital monitoring, and design optimization promise to further enhance their performance, ensuring that they remain indispensable tools in high-pressure applications. By keeping an eye on emerging trends and continuously learning from past experiences, the engineering community is well on its way to developing the next generation of pumping solutions.
Why It Matters
At its core, the study of the working principle of vertical multistage pumps is about more than just understanding machinery—it’s about appreciating the thoughtful integration of design, science, and practical application. Whether you’re involved in engineering, facility management, or simply have a passion for technology, gaining insight into these systems can broaden your perspective on how everyday technologies are designed to meet complex demands.
Your Role as a Learner and Innovator
Every technological advancement starts with curiosity and a willingness to understand the underlying principles. As you learn more about vertical multistage pumps, consider how these principles might apply to other areas of technology or even inspire innovative solutions in your own work or daily life. The world of fluid dynamics is vast, and the concepts behind these pumps have applications far beyond what meets the eye.
In Summary
-
Step-by-Step Pressure Build-up: The incremental pressure increase in each stage of the pump is what makes vertical multistage pumps uniquely effective.
-
Efficiency and Reliability: Through thoughtful design and robust engineering, these pumps deliver high performance with minimal energy loss.
-
Wide-ranging Applications: From municipal water supply to industrial processes, the versatility of vertical multistage pumps is evident in their numerous applications.
-
A Future of Innovation: Advances in technology and materials promise to push the boundaries of what vertical multistage pumps can achieve, paving the way for even more efficient and sustainable solutions.
Vertical multistage pumps are not just machines; they are integral parts of the infrastructure that keeps our modern world running smoothly. Their design and operation reflect a deep understanding of fluid dynamics and mechanical engineering—a perfect example of how small, precise steps can lead to monumental results.
Conclusion
In this detailed exploration of the working principle of vertical multistage pumps, we have journeyed through the fundamentals of their design, operation, and the myriad benefits they offer. We started with a historical perspective, understanding how pump technology evolved to meet increasing demands for high-pressure applications. We then broke down the pump’s operation into clear, manageable stages, highlighting the crucial roles played by impellers and diffusers.
The discussion of key components such as pump casings, suction and discharge nozzles, and mechanical seals underscores the complexity and precision required in pump design. We also delved into the challenges faced by these systems, including cavitation and component wear, and provided actionable maintenance tips to ensure long-lasting performance.
Looking ahead, innovations in digitalization, advanced materials, and sustainable engineering are set to revolutionize the way vertical multistage pumps are designed and operated. These advances not only promise improved efficiency and reduced energy consumption but also align with broader efforts toward environmental sustainability.
Ultimately, the study of vertical multistage pumps serves as a reminder that even the most complex industrial systems are built on the foundation of simple, incremental improvements. Much like the steps we take in our daily lives to achieve greater goals, each stage of a vertical multistage pump contributes to a final output that is far greater than the sum of its parts.
By understanding the working principle of vertical multistage pumps, you gain insight into a critical piece of technology that impacts everything from urban water distribution to industrial processing. This knowledge can empower you to appreciate the engineering behind these systems, inspire innovation, and foster a deeper understanding of how modern technology is applied to solve real-world challenges.
Thank you for joining us on this in-depth exploration. We hope this post has shed light on the intricacies of vertical multistage pumps and has provided you with the clarity needed to appreciate their vital role in our modern world. Whether you are an engineer, a facility manager, or simply someone with a keen interest in technology, the lessons learned from these pumps offer valuable insights into the art and science of mechanical innovation.
This blog post is designed to be a comprehensive, humanized guide to understanding the working principle of vertical multistage pumps. We’ve strived to maintain originality, clarity, and relatability throughout this piece, ensuring that both technical experts and curious minds can gain a meaningful understanding of these remarkable devices.
Additional Resources
If you’re eager to delve even deeper into the topics discussed, consider exploring the following resources:
-
Technical Journals: Academic publications and engineering journals often feature detailed studies on fluid dynamics and pump design. These can provide further insight into the latest research and technological advancements in the field.
-
Industry Conferences: Attending industry conferences or webinars focused on pump technology and industrial fluid dynamics can offer practical knowledge and networking opportunities with experts.
-
Manufacturer White Papers: Many pump manufacturers publish detailed white papers that discuss the design, operation, and maintenance of vertical multistage pumps. These documents can be a valuable resource for both theoretical knowledge and practical application tips.
Final Reflections
Understanding the working principle of vertical multistage pumps is a journey into the heart of fluid dynamics and mechanical engineering. From the humble beginnings of early pump designs to today’s advanced, high-pressure systems, the evolution of pump technology reflects our ongoing quest for efficiency, reliability, and innovation. By appreciating the step-by-step process by which these pumps operate, we can better understand the intricate balance of forces that make modern engineering so effective.
Vertical multistage pumps exemplify the beauty of incremental progress—a process where every stage, every carefully designed component, plays a crucial role in delivering high-pressure, reliable performance. This approach, rooted in both theory and practice, serves as a powerful reminder of the importance of meticulous engineering and continuous improvement.
We hope that this in-depth exploration has not only informed you about the technical aspects but has also inspired you to see the value in the details. The same principles that govern the operation of vertical multistage pumps can be applied to many areas of life, reminding us that sometimes, the most significant achievements come from the accumulation of many small, thoughtful steps.
By embracing both the art and science of pump technology, we can look forward to a future where efficiency, sustainability, and innovation continue to drive progress. Vertical multistage pumps are just one example of how thoughtful design can transform everyday challenges into opportunities for improvement.
Thank you for reading this extensive guide on understanding the working principle of vertical multistage pumps. We invite you to share your thoughts, experiences, or questions in the comments section below—let’s continue the conversation on how these incredible machines power our modern world.