Contents
- 1 Introduction
- 2 The Role of Coolant Pumps
- 3 Basic Principles: How Coolant Pumps Work
- 4 Components of Coolant Pumps
- 5 Types of Coolant Pumps
- 6 Operation Cycle: A Step-by-Step Walkthrough
- 7 Why Coolant Pumps Matter
- 8 Common Issues and Troubleshooting
- 9 Maintenance Tips for Coolant Pumps
- 10 Coolant Pumps in Different Applications
- 11 The Future of Coolant Pump Technology
- 12 Practical Examples: Real-World Applications of Coolant Pumps
- 13 How to Choose the Right Coolant Pump
- 14 Common Myths and Misconceptions
- 15 The Human Side: Personal Experiences with Coolant Pumps
- 16 Environmental and Economic Impact
- 17 Frequently Asked Questions (FAQs)
- 18 Integrating Coolant Pumps with Overall Engine Management
- 19 Tips for DIY Enthusiasts
- 20 Conclusion
Cooling systems are the unsung heroes in many machines and vehicles, quietly ensuring that everything stays within safe operating temperatures. In today’s post, we’ll take a deep dive into how coolant pumps work. Whether you’re a car enthusiast, a DIY mechanic, or simply curious about how your machine stays cool, this post will provide an in-depth, relatable explanation of coolant pumps and their role in keeping systems running efficiently.
Introduction
Every engine, whether in your car, your computer, or industrial machinery, requires an efficient cooling system. At the heart of these systems are the often-overlooked coolant pumps. These pumps ensure that coolant fluid continuously circulates, removing excess heat and maintaining the ideal operating temperature for your system. In this comprehensive guide, we’ll explore what coolant pumps are, dive into the mechanics of how coolant pumps work, and examine why they’re essential.
Imagine your engine as a bustling city on a hot summer day. Just as a city relies on its water supply and air conditioning to keep life going smoothly, an engine depends on its coolant pump to manage heat and ensure optimal performance. By the end of this post, you’ll have a clear understanding of the inner workings of these devices, their importance, and how to maintain them for long-lasting reliability.
The Role of Coolant Pumps
Before we explore the nitty-gritty of how coolant pumps work, it’s important to understand why they’re so vital in various systems.
Keeping Things Cool
At their core, coolant pumps are designed to move coolant fluid through a system. The coolant absorbs heat from critical components like the engine block, radiators, and other heat-generating parts, then transfers that heat away to be dissipated. This process prevents overheating, which can lead to severe damage and reduced efficiency.
Enhancing Efficiency
Coolant pumps play a critical role in enhancing overall system efficiency. By maintaining a stable temperature, these pumps ensure that engines and machinery operate at peak performance. This can result in better fuel economy in vehicles, improved processing speeds in computers, and more reliable performance in industrial equipment.
Preventing Wear and Tear
Constant and effective cooling helps to reduce the stress on various components. Overheating can cause parts to warp, crack, or fail entirely. Coolant pumps help to prolong the lifespan of your system by mitigating these risks, ensuring smoother operation and reducing the need for costly repairs.
Basic Principles: How Coolant Pumps Work
Understanding how coolant pumps work starts with understanding the basic principles of fluid dynamics and thermodynamics. Let’s break it down into easy-to-understand components.
Fluid Circulation
Coolant pumps are essentially designed to push or pull a fluid through a system. They create a continuous flow of coolant, ensuring that every part of the system receives the necessary cooling. In many applications, this involves a closed-loop system where the same coolant circulates repeatedly.
Heat Absorption and Transfer
The primary function of the coolant is to absorb heat. When the fluid passes through the engine or other heat-generating parts, it picks up heat and increases in temperature. The pump then moves this heated fluid to a radiator or heat exchanger, where the heat is dissipated into the surrounding environment. The now-cooled fluid is circulated back to the engine to repeat the process.
Pressure and Flow Rate
A critical factor in how coolant pumps work is the generation of sufficient pressure to circulate the coolant efficiently. The pump’s design ensures that there is enough force to move the coolant through narrow passages and around obstacles. The flow rate, determined by the pump’s power and design, directly impacts the effectiveness of the cooling system. A higher flow rate can remove more heat quickly, but it also requires more energy and precision in design.
Energy Conversion
Coolant pumps convert mechanical energy into hydraulic energy. This conversion process is fundamental: as the pump’s impeller rotates (or, in some designs, another moving part), it imparts kinetic energy to the coolant. This kinetic energy is then converted into pressure energy as the coolant moves through the system. Understanding this energy conversion is key to appreciating the efficiency and importance of these pumps.
Analogies for Clarity
Imagine a water park where water is pumped through slides and rides. The pump (like the heart of the park’s system) ensures that water flows at just the right speed and pressure so that visitors enjoy a smooth ride without being knocked over by unexpected gushes. In a similar fashion, coolant pumps ensure that the coolant flows steadily, keeping the engine at a safe operating temperature.
Components of Coolant Pumps
Delving deeper into the details, let’s explore the key components that make up a coolant pump. Each of these parts plays a specific role in ensuring the pump’s overall functionality.
1. The Impeller
The impeller is the heart of most coolant pumps. This rotating component is responsible for moving the coolant fluid by creating a centrifugal force. As the impeller spins, it draws coolant into the center and flings it outward, creating the flow that circulates the coolant throughout the system.
- Design Variations: Depending on the application, impellers may be designed with different shapes and sizes. Some are optimized for high flow rates, while others prioritize high pressure.
- Materials: Impellers are often made from durable metals or high-strength plastics, designed to withstand constant rotation and exposure to various chemical additives present in the coolant.
2. The Housing
The housing encases the impeller and directs the flow of coolant. It ensures that the moving fluid is guided efficiently from the pump’s inlet to its outlet.
- Flow Channels: The design of the housing can greatly influence the pump’s efficiency. Well-designed flow channels reduce turbulence and help maintain a smooth, consistent flow.
- Seal Integrity: A robust housing also plays a role in preventing leaks. Seals and gaskets are often integrated into the housing design to maintain a closed system.
3. The Drive Mechanism
The drive mechanism is responsible for powering the impeller. In many systems, this is achieved via a belt-driven system or a direct coupling to the engine’s crankshaft.
- Belt-Driven Pumps: These use a belt to transfer power from the engine to the pump, which can allow for flexible placement and easy maintenance.
- Electric Pumps: Increasingly common in modern designs, electric coolant pumps are powered by an electric motor, offering improved efficiency and control, especially in vehicles with stop-start systems.
4. Seals and Bearings
To keep the system running smoothly, seals and bearings play an essential role in minimizing friction and preventing leaks. Seals ensure that the coolant does not escape the pump housing, while bearings support the impeller’s rotation, reducing wear over time.
- Maintenance Concerns: Over time, seals and bearings may wear out, leading to potential leaks or decreased efficiency. Regular inspection and maintenance are crucial for optimal pump performance.
5. Sensors and Controls
In modern systems, sensors and control units are often integrated with coolant pumps. These sensors monitor coolant flow, temperature, and pressure, providing real-time data to the vehicle’s computer system. This allows for dynamic adjustments, ensuring the pump operates under optimal conditions at all times.
- Integration with Engine Management: By linking the coolant pump’s operation to the engine management system, modern vehicles can optimize engine performance and reduce fuel consumption.
- Adaptive Control: Electric coolant pumps often come with adaptive control features that adjust the pump speed based on the current cooling demand, further enhancing efficiency.
Types of Coolant Pumps
Not all coolant pumps are created equal. Depending on the application and design requirements, several types of coolant pumps are used in different systems. Here, we’ll examine some of the most common types and their applications.
Mechanical (Belt-Driven) Coolant Pumps
Mechanical coolant pumps have been a staple in automotive engines for decades. They are directly powered by the engine via a belt and are known for their reliability and simplicity.
- Advantages:
- Proven technology with decades of use.
- Simple design that is easy to repair.
- Reliable performance under a wide range of operating conditions.
- Disadvantages:
- Tied directly to engine speed, meaning performance can vary with RPM.
- Belt wear and potential for misalignment can affect performance over time.
Electric Coolant Pumps
Electric coolant pumps are becoming increasingly popular, especially in modern vehicles that require more precise control over coolant flow. These pumps operate independently of engine speed, offering several advantages.
- Advantages:
- More precise control over coolant flow.
- Can operate continuously even when the engine is off (useful for maintaining optimal engine temperature during idle periods or in hybrid vehicles).
- Reduced parasitic losses since they’re not mechanically driven.
- Disadvantages:
- Higher initial cost due to more complex components.
- Dependence on the electrical system means that issues with wiring or power supply can affect operation.
Hydraulic Coolant Pumps
Hydraulic coolant pumps are used in specialized industrial applications where high pressure is required. These pumps are designed to handle demanding conditions and can often be found in heavy machinery and equipment.
- Advantages:
- Capable of generating very high pressures.
- Durable and built to withstand harsh operating environments.
- Disadvantages:
- More complex and expensive than typical automotive coolant pumps.
- Require specialized maintenance and repairs.
Submersible Coolant Pumps
Submersible pumps are designed to be fully immersed in the coolant fluid. They are commonly used in computer cooling systems and other electronic applications where space is limited and noise reduction is important.
- Advantages:
- Operate quietly due to reduced vibration.
- Compact design ideal for confined spaces.
- Disadvantages:
- May be more challenging to service due to their sealed design.
- Typically used in lower-power applications compared to automotive pumps.
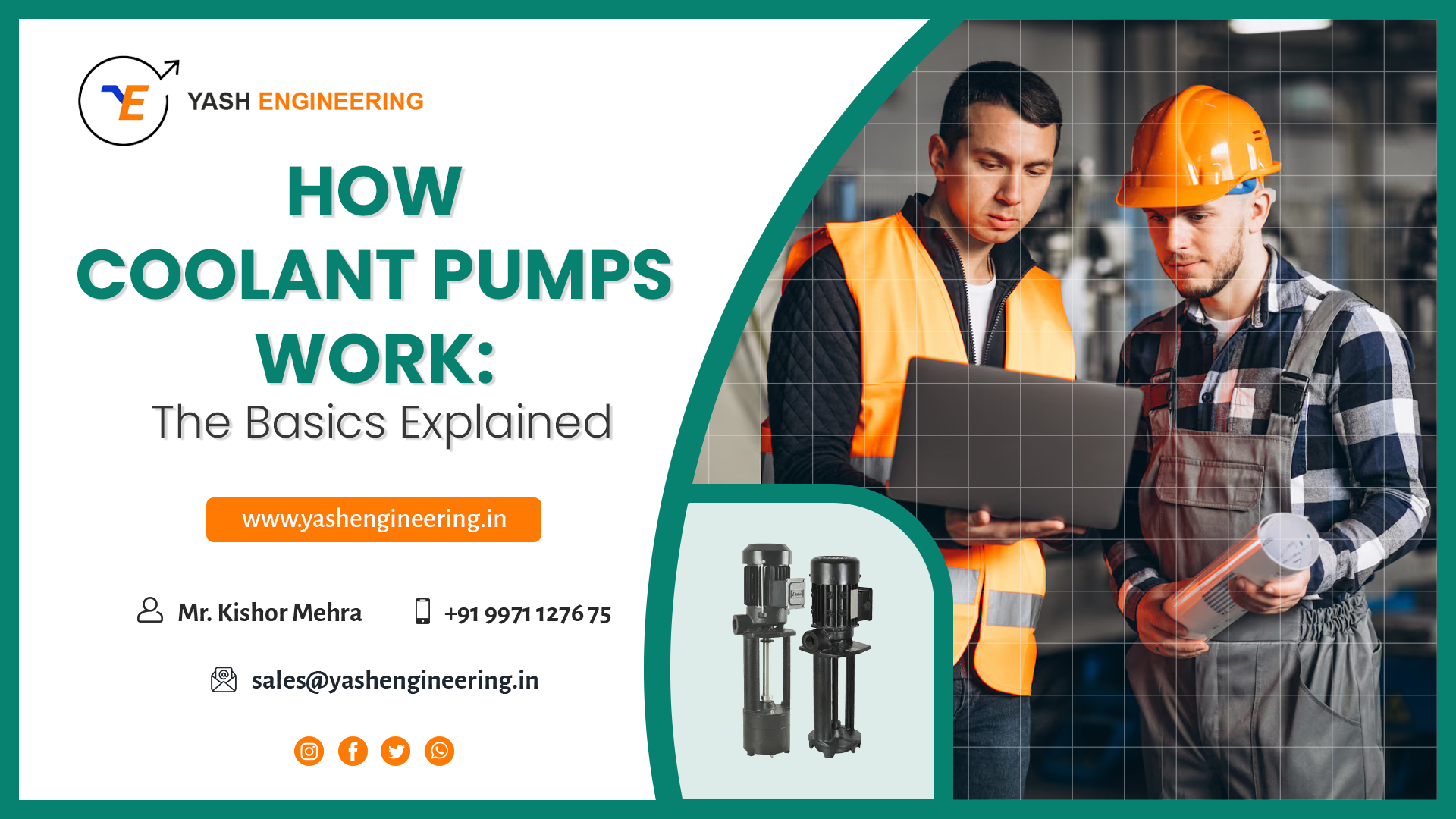
Operation Cycle: A Step-by-Step Walkthrough
Understanding how coolant pumps work can be made clearer by breaking down the operation cycle into several steps. Here’s a step-by-step walkthrough of a typical coolant pump’s operation:
Step 1: Coolant Intake
The cycle begins with the coolant pump drawing in coolant fluid from the engine block or reservoir. As the impeller rotates, it creates a low-pressure area at the pump’s inlet, causing the fluid to be drawn in. This step is critical, as any obstruction or leak at this stage can lead to reduced flow and potential overheating.
Step 2: Acceleration of Coolant
Once the coolant enters the pump housing, the impeller rapidly rotates to accelerate the fluid. The design of the impeller channels the fluid outward through centrifugal force, significantly increasing its speed and pressure. The acceleration process is finely tuned to ensure that the coolant reaches the necessary velocity to overcome system resistance.
Step 3: Coolant Discharge
The accelerated coolant is then forced out of the pump through the outlet. This high-pressure fluid is directed towards the radiator or heat exchanger. In some systems, multiple outlets may be present to distribute the coolant evenly across various components. This discharge stage is where the coolant picks up heat from the engine and begins its journey through the system.
Step 4: Heat Exchange
Upon reaching the radiator or heat exchanger, the heated coolant flows through a network of tubes or channels. As air passes over these tubes, the coolant releases its absorbed heat, cooling down in the process. The effectiveness of this heat exchange is a key factor in the overall efficiency of the cooling system.
Step 5: Return to the Engine
After releasing its heat, the cooled coolant returns to the engine or the starting reservoir to begin the cycle again. This continuous loop ensures that the engine remains within a safe operating temperature, even under demanding conditions.
The Continuous Nature of the Cycle
It’s important to note that this operation cycle is continuous. The coolant pump never really “stops” in a well-functioning system; it simply maintains a constant flow to keep the engine cool. This cycle is a great example of energy conversion and the laws of thermodynamics in action. Every step in the process, from intake to heat exchange, is carefully engineered to maximize efficiency and reliability.
Why Coolant Pumps Matter
Understanding how coolant pumps work is essential, not just for mechanics or engineers, but for anyone who relies on machines that generate heat. Here are some compelling reasons why coolant pumps are so crucial:
1. Preventing Overheating
The primary purpose of coolant pumps is to prevent overheating. When an engine or machine overheats, it can lead to catastrophic failure, costly repairs, or even complete breakdown. Coolant pumps ensure that heat is consistently removed from the system, keeping temperatures at safe levels.
2. Enhancing Performance
A well-cooled engine performs better. For automobiles, this means more efficient combustion, smoother acceleration, and better overall performance. For industrial machinery, it translates to increased productivity and a longer operational lifespan. The direct link between temperature regulation and performance cannot be overstated.
3. Environmental Benefits
Efficient cooling systems contribute to environmental sustainability. By maintaining optimal temperatures, engines can run more efficiently, reducing fuel consumption and lowering emissions. This is particularly important in today’s world, where environmental considerations are a top priority.
4. Cost Savings
Investing in a reliable coolant pump can lead to significant long-term savings. Preventative maintenance that includes regular checks on your coolant pump can avoid expensive repairs or engine replacements. In many cases, a small investment in quality coolant pumps pays off in reduced downtime and maintenance costs.
5. Safety Considerations
In certain applications, especially in industrial settings, overheating can pose serious safety risks. A malfunctioning coolant pump may lead to uncontrolled heat build-up, increasing the risk of fires or hazardous material leaks. Thus, ensuring that coolant pumps are working efficiently is a critical safety measure.
Common Issues and Troubleshooting
Even the best-designed coolant pumps can run into issues over time. Understanding these potential problems can help you troubleshoot and maintain your system before minor issues escalate into major failures.
1. Reduced Flow Rate
Symptoms:
- Engine running hotter than normal.
- Inconsistent temperature readings.
- Unusual noise from the pump.
Causes:
- Clogging or blockage in the pump or hoses.
- Worn-out impeller.
- Air leaks in the system.
Troubleshooting Tips:
- Check for debris or blockage in the pump and hoses.
- Inspect the impeller for signs of wear or damage.
- Ensure all connections are sealed and secure.
2. Leaks and Seal Failures
Symptoms:
- Visible coolant leakage around the pump housing.
- Low coolant levels.
- Puddles or drips under the machine or vehicle.
Causes:
- Deteriorated seals or gaskets.
- Cracks in the pump housing.
- Corrosion from coolant additives.
Troubleshooting Tips:
- Inspect seals and replace them if they show signs of wear.
- Check the pump housing for any visible cracks.
- Maintain proper coolant composition to minimize corrosion.
3. Unusual Noises
Symptoms:
- Squeaking or grinding sounds coming from the pump.
- Vibrations felt through the engine or machinery.
Causes:
- Worn bearings.
- Debris caught in the pump mechanism.
- Imbalanced impeller.
Troubleshooting Tips:
- Inspect and replace bearings if necessary.
- Clean the pump internals to remove any debris.
- Ensure the impeller is balanced and free of damage.
4. Overheating Despite Functioning Pump
Symptoms:
- Engine or system still running hot even when the pump appears to be working.
- Frequent activation of cooling fans without temperature drop.
Causes:
- Blocked radiator or heat exchanger.
- Faulty thermostat.
- Air pockets in the cooling system.
Troubleshooting Tips:
- Flush the system to remove air pockets.
- Check the radiator and clean any blockages.
- Test the thermostat and replace if necessary.
Maintenance Tips for Coolant Pumps
Just as regular oil changes and tire rotations keep your vehicle running smoothly, routine maintenance of coolant pumps is essential. Here are some maintenance tips to help extend the life of your pump and ensure optimal performance:
1. Regular Inspections
- Frequency: Schedule regular inspections, especially if your vehicle or machinery is older.
- What to Look For: Check for signs of wear on the impeller, leaks around the pump housing, and any unusual noises during operation.
- Professional Help: If you’re not comfortable performing these inspections yourself, consult with a professional mechanic or technician.
2. Cleaning the System
- Flushing the Coolant: Over time, debris and sediment can accumulate in the cooling system. Regularly flushing the coolant can help prevent blockages and maintain a smooth flow.
- Replacing Coolant: Follow the manufacturer’s recommendations for coolant replacement intervals to ensure that the fluid remains effective in heat absorption.
3. Seal and Bearing Replacement
- Proactive Replacement: Seals and bearings can wear out with time and should be replaced proactively, not just when a leak or noise occurs.
- Quality Parts: Always use high-quality replacement parts that match the specifications of your original pump to maintain performance and durability.
4. Monitor Temperature Readings
- Dashboard Gauges: For vehicles, keep an eye on the temperature gauge. Sudden spikes or gradual increases can indicate an issue with the coolant pump.
- Digital Sensors: In modern systems, digital sensors provide real-time feedback on coolant flow and temperature. Use these diagnostics to monitor the health of your system.
5. Professional Servicing
- Scheduled Maintenance: Incorporate coolant pump checks into your regular service schedule.
- Diagnostic Tools: Use advanced diagnostic tools to detect potential issues early on, ensuring that small problems don’t turn into major failures.
Coolant Pumps in Different Applications
While our discussion has largely centered around automotive applications, coolant pumps play an essential role in a wide range of systems. Let’s explore a few different applications where understanding how coolant pumps work is equally valuable.
1. Automotive Cooling Systems
- Internal Combustion Engines: Most cars and trucks use a belt-driven or electric coolant pump to manage the heat generated during combustion. The pump circulates a mixture of water and antifreeze, ensuring the engine stays within safe operating temperatures.
- Hybrid and Electric Vehicles: Modern vehicles are incorporating advanced electric coolant pumps that can adjust flow rates based on real-time data, contributing to both improved efficiency and reduced emissions.
2. Computer and Data Center Cooling
- Liquid Cooling Systems: High-performance computers and data centers often use liquid cooling systems to manage the heat generated by processors and other electronic components. Submersible coolant pumps in these systems are prized for their quiet operation and compact design.
- Precision Control: These systems often include sensors that monitor temperature, allowing for fine-tuned adjustments to the pump’s operation to maintain an optimal balance between cooling performance and energy consumption.
3. Industrial Machinery
- Heavy Equipment: Industrial machines, including manufacturing robots, CNC machines, and large generators, rely on robust coolant pumps to handle high thermal loads. Hydraulic coolant pumps are common in these applications due to their ability to generate high pressures.
- Safety and Reliability: In industrial settings, a failure in the cooling system can result in dangerous operating conditions. Therefore, regular maintenance and robust design are critical to ensuring operational safety and reliability.
4. Renewable Energy Systems
- Solar Thermal and Geothermal Systems: Coolant pumps are also used in renewable energy applications, such as solar thermal power plants and geothermal energy systems. In these contexts, the pumps help transfer heat to or from a storage system, maximizing the efficiency of the renewable energy cycle.
- Sustainable Design: The integration of coolant pumps in these systems underscores the importance of effective thermal management in promoting energy efficiency and reducing the environmental impact of power generation.
The Future of Coolant Pump Technology
As technology advances, the design and functionality of coolant pumps continue to evolve. Innovations in materials, design, and control systems are poised to further improve efficiency, reduce maintenance requirements, and enhance overall performance.
1. Integration with Smart Systems
Future coolant pumps are likely to be even more integrated with smart monitoring systems. Advances in sensor technology and artificial intelligence could lead to predictive maintenance, where the pump can alert you to potential issues before they become serious problems. This integration can help optimize performance and extend the lifespan of the cooling system.
2. Energy Efficiency and Sustainability
With a growing focus on sustainability, future designs will likely emphasize lower energy consumption. Electric coolant pumps, in particular, are expected to become more efficient through improvements in motor design and control algorithms. This shift will be crucial in reducing the overall environmental impact of vehicles and industrial systems.
3. Advanced Materials
Materials science is playing a significant role in the future of coolant pumps. Innovations in high-strength polymers and lightweight metals may lead to pumps that are both more durable and less energy-intensive. These new materials can also contribute to more compact designs, which is particularly important in applications with space constraints.
4. Customizable Flow Control
As systems become more complex, the need for precise, customizable flow control will increase. Future coolant pumps may offer adaptive flow control, adjusting dynamically to the system’s requirements. This can be particularly useful in hybrid and electric vehicles, where optimal temperature regulation directly impacts performance and battery efficiency.
5. Enhanced Reliability
Advancements in design and manufacturing are likely to yield pumps with longer service lives and lower failure rates. With enhanced diagnostics and self-monitoring capabilities, these pumps will provide increased reliability, reducing downtime and maintenance costs in both automotive and industrial applications.
Practical Examples: Real-World Applications of Coolant Pumps
To better understand how coolant pumps work and why they are so critical, let’s look at a few real-world examples and scenarios:
Example 1: The Everyday Car
Imagine you’re driving on a hot summer day. Your car’s engine is working hard, and temperatures are rising. Thanks to the coolant pump, coolant fluid circulates from the engine to the radiator, where the heat is dissipated. The result? Your engine remains cool, allowing you to drive safely without the fear of overheating. This scenario highlights the everyday importance of a well-functioning coolant pump, as even a minor failure can lead to engine damage and costly repairs.
Example 2: A High-Performance Racing Car
In a racing environment, every fraction of a degree matters. High-performance vehicles use advanced coolant pumps—often electric in nature—to manage extremely high thermal loads. The pumps adjust in real-time to ensure optimal coolant flow, even during sudden acceleration or braking. This dynamic control is crucial to maintain performance and prevent engine degradation under intense conditions.
Example 3: Industrial Machinery in a Factory
Consider a factory floor where heavy machinery operates continuously. The equipment generates enormous amounts of heat, and a failure in the cooling system could result in production halts or even hazardous conditions. Coolant pumps in this setting are built to handle high pressures and constant use, ensuring that the machinery operates safely and efficiently around the clock.
Example 4: Data Centers and Server Farms
In data centers, maintaining the optimal temperature is key to preventing hardware failures and ensuring uptime. Liquid cooling systems equipped with submersible coolant pumps provide a silent and efficient solution to manage the heat produced by high-performance computing systems. This application shows how coolant pumps are not just for vehicles but are indispensable in modern technology infrastructures.
How to Choose the Right Coolant Pump
When it comes to replacing or upgrading your coolant pump, several factors come into play. Here are some tips to help you choose the right pump for your needs:
1. Application Requirements
- Vehicle vs. Industrial: Determine whether the pump will be used in an automotive application, industrial machinery, or another system. Each application may require different flow rates, pressures, and durability standards.
- Environmental Conditions: Consider the operating environment. For instance, pumps in extreme temperature environments may need special materials or enhanced cooling features.
2. Pump Type
- Mechanical vs. Electric: Decide whether a mechanical (belt-driven) or electric pump is more suitable for your application. Electric pumps offer more precise control and can operate independently of engine speed, while mechanical pumps are simpler and have a long track record of reliability.
- Hydraulic or Submersible Options: For specialized applications, look into hydraulic or submersible pumps that are designed to meet specific performance criteria.
3. Maintenance and Durability
- Ease of Service: Evaluate how easy it is to service the pump. Pumps that offer modular designs can be easier to repair and maintain.
- Component Quality: Look for pumps made from high-quality materials with robust seals and bearings, as these components are critical to long-term performance.
4. Cost vs. Performance
- Budget Considerations: While high-end pumps may offer superior performance, they also come with a higher price tag. Assess the balance between cost and performance to find the pump that best meets your needs.
- Long-Term Investment: Remember that investing in a quality pump can lead to long-term savings by reducing maintenance costs and improving system efficiency.
Common Myths and Misconceptions
Despite their widespread use, several myths surround coolant pumps. Let’s debunk some common misconceptions:
Myth 1: “Coolant Pumps Are Only Necessary for Hot Climates”
While it’s true that engines in hot climates may experience more stress, coolant pumps are essential in all operating conditions. Even in cooler climates, engines generate significant heat, and without an effective coolant pump, overheating and performance issues can occur.
Myth 2: “All Coolant Pumps Are the Same”
There is a wide variety of coolant pumps available, each designed for different applications and performance requirements. The differences in design—whether mechanical, electric, hydraulic, or submersible—mean that not all coolant pumps function the same way or offer the same level of performance.
Myth 3: “A Failing Coolant Pump Always Makes Loud Noises”
While unusual noises can be a sign of a failing pump, some issues may occur without any audible warning. Regular maintenance and inspections are key, as a pump can suffer from reduced flow or minor leaks without obvious symptoms until the problem escalates.
Myth 4: “Coolant Pumps Can Fix Themselves”
Modern systems with smart sensors and diagnostics may alert you to potential issues, but a coolant pump will not fix itself. Proactive maintenance is required to ensure that any developing issues are addressed before they lead to major failures.
The Human Side: Personal Experiences with Coolant Pumps
Understanding the technical details of how coolant pumps work is important, but so is appreciating the personal stories and experiences that highlight their value. Let’s look at a few anecdotes that underscore the human side of coolant pump maintenance and repair.
A Mechanic’s Tale
Joe, a seasoned mechanic with over 20 years of experience, recalls a time when a customer’s vehicle was suffering from intermittent overheating. After a thorough inspection, Joe discovered that the coolant pump was partially blocked by sediment—a common issue in older vehicles. With a careful cleaning and replacement of worn seals, the vehicle’s performance improved dramatically. Joe emphasizes that regular maintenance can save you from costly repairs and unexpected breakdowns.
A Racer’s Experience
For competitive racers, every second counts. Sarah, a professional racing driver, shares that her team recently upgraded to an advanced electric coolant pump. The new pump offered real-time adaptive control, allowing her engine to maintain peak performance even during intense races. Sarah highlights that the investment in a high-quality coolant pump not only improved her car’s performance but also provided peace of mind on the track.
The Data Center Manager
In a large data center, managing heat is a daily challenge. Mark, the facility manager, explains that their move to a liquid cooling system with submersible coolant pumps has drastically reduced energy consumption and hardware failures. The quieter, more efficient cooling system has made the data center a more reliable and comfortable environment for both machines and the people who work there.
Environmental and Economic Impact
Reducing Emissions
An often-overlooked benefit of an efficiently working coolant pump is its impact on fuel efficiency and emissions. When an engine is properly cooled, it runs more efficiently, reducing fuel consumption and lowering harmful emissions. This is particularly significant in today’s climate-conscious world where even small improvements in efficiency can have a cumulative environmental impact.
Lower Operating Costs
From an economic perspective, a well-maintained cooling system translates to lower operating costs. Vehicles with efficient coolant pumps tend to have fewer breakdowns and require less frequent repairs. In industrial applications, the reliability of coolant pumps can mean the difference between smooth operations and costly downtime.
Contribution to Renewable Energy Efficiency
In renewable energy applications, such as solar thermal power plants, coolant pumps contribute directly to the efficiency of the energy conversion process. By optimizing the transfer of heat, these pumps help maximize the output of renewable energy systems, promoting a cleaner, more sustainable energy future.
Frequently Asked Questions (FAQs)
Q1: What are the signs of a failing coolant pump?
A: Some common signs include reduced coolant flow, overheating, unusual noises, and visible coolant leaks. Regular maintenance and inspection can help detect these issues early.
Q2: How often should I replace or service my coolant pump?
A: It depends on the application and usage. For vehicles, following the manufacturer’s recommended service intervals is best. In industrial settings, periodic inspections and proactive replacement of worn components can extend the pump’s lifespan.
Q3: Are electric coolant pumps better than mechanical ones?
A: Electric coolant pumps offer precise control and improved efficiency, particularly in modern vehicles with variable operating conditions. However, mechanical pumps are proven, reliable, and simpler in design. The choice depends on your specific needs and application.
Q4: Can I replace a coolant pump myself?
A: While some experienced DIY mechanics may handle basic pump replacements, many modern systems are complex and may require specialized tools and diagnostics. When in doubt, it’s wise to consult a professional.
Integrating Coolant Pumps with Overall Engine Management
The Bigger Picture
A coolant pump doesn’t work in isolation. It’s part of a broader system designed to optimize engine performance and longevity. Modern vehicles and industrial systems integrate coolant pumps with engine control units (ECUs), sensors, and even computer-aided diagnostics. This integration ensures that the pump operates under the best conditions possible, adapting to changes in engine load and external temperatures.
Smart Cooling Systems
With the advent of smart technology, many systems now feature adaptive cooling mechanisms. For instance, electric coolant pumps can adjust their operation based on real-time data, providing just the right amount of cooling when needed. This not only improves performance but also contributes to fuel economy and reduces wear on other engine components.
The Role of Data Analytics
In industrial applications, data analytics play a crucial role. Sensors throughout the cooling system can detect anomalies and predict potential failures before they occur. By analyzing trends in temperature, pressure, and flow rate, technicians can perform predictive maintenance, ensuring that the coolant pump—and by extension, the entire system—remains in optimal condition.
Tips for DIY Enthusiasts
If you’re a DIY enthusiast looking to understand and possibly work on your own coolant pump, here are some practical tips:
1. Educate Yourself
Before attempting any repairs, educate yourself about your specific coolant pump model. Read the owner’s manual, watch tutorial videos, and join online forums where professionals and enthusiasts share advice and troubleshooting tips.
2. Gather the Right Tools
Having the right tools is crucial. Depending on your system, you may need specialized wrenches, seal extractors, or diagnostic tools. Investing in quality tools will make your job easier and help avoid damaging sensitive components.
3. Document Your Work
If you plan to work on your coolant pump, take photos or notes during the disassembly process. This documentation can be invaluable when it comes time to reassemble everything correctly.
4. Safety First
Always ensure that the engine is cool and that you have disconnected the battery (in vehicles) before beginning any repairs. Safety should always be your top priority.
5. Know When to Call a Professional
While DIY projects can be rewarding, don’t hesitate to call a professional if you encounter unexpected issues or if the system appears more complex than anticipated. Sometimes, the cost of a mistake can far outweigh the savings of a DIY fix.
Conclusion
Coolant pumps play a vital role in maintaining the efficiency, performance, and longevity of engines and machinery. By understanding how coolant pumps work, we gain insight into a critical component that ensures our vehicles and industrial systems operate smoothly, safely, and efficiently.
In this post, we explored the essential principles of fluid circulation, heat absorption, and energy conversion that underlie the operation of coolant pumps. We examined the key components—such as the impeller, housing, drive mechanism, seals, and sensors—and discussed the different types of pumps used in various applications. From mechanical and electric pumps in automotive systems to hydraulic and submersible designs in industrial and computer cooling systems, the diversity of coolant pump designs underscores their importance across many fields.
We also discussed common issues, maintenance tips, and real-world examples that illustrate the human side of working with coolant pumps. Whether you’re a mechanic, an engineer, or simply curious about the technology that keeps your engine cool, understanding these systems can help you appreciate the ingenuity behind them and the role they play in our everyday lives.
As technology continues to advance, we can expect coolant pumps to become even more integrated with smart systems, more energy-efficient, and more reliable. With innovations in materials and design, future coolant pumps will likely offer even greater performance while reducing environmental impacts and operating costs.
Remember, a well-maintained coolant pump is not just a component of your vehicle or machinery—it’s a critical guardian against overheating, a key contributor to efficiency, and an essential part of ensuring long-term operational success.
Thank you for taking the time to read this in-depth exploration of how coolant pumps work. I hope this guide has provided you with a clearer understanding of the technology that keeps our engines cool and our systems running smoothly. Whether you’re maintaining your own vehicle or working in an industrial setting, the principles and practices discussed here can help you make informed decisions and ensure that your cooling system operates at its best.
Stay cool and keep your machines running efficiently!