Contents
- 1 Introduction
- 2 Understanding Horizontal Multistage End Suction Pumps
- 3 Advantages of Horizontal Multistage End Suction Pumps
- 3.1 1. High Efficiency and Superior Performance
- 3.2 2. Compact and Space-Saving Design
- 3.3 3. Enhanced Reliability and Durability
- 3.4 4. Ease of Maintenance
- 3.5 5. Versatile Applications
- 3.6 6. Energy Efficiency and Cost Savings
- 3.7 7. Improved Process Control
- 3.8 8. Lower Noise Levels and Vibrations
- 3.9 9. Cost-Effective Over the Long Term
- 3.10 10. Customizable to Specific Needs
- 4 Technical Insights: How Horizontal Multistage End Suction Pumps Achieve Superior Performance
- 5 Real-World Applications: Case Studies and Industry Examples
- 6 Future Trends and Innovations
- 7 Practical Tips for Choosing the Right Pump
- 8 Integration and Installation: Getting the Most Out of Your Pump
- 9 The Human Side of Industrial Pumping
- 10 In-Depth Technical Comparisons
- 11 Environmental Considerations and Sustainability
- 12 Lessons Learned from Industry Veterans
- 13 Frequently Asked Questions
- 13.1 Q1: What makes horizontal multistage end suction pumps different from other pump types?
- 13.2 Q2: How do these pumps contribute to energy efficiency?
- 13.3 Q3: Are horizontal multistage end suction pumps difficult to install?
- 13.4 Q4: What kind of maintenance do these pumps require?
- 13.5 Q5: In what industries are these pumps most commonly used?
- 14 Conclusion
- 15 Final Thoughts
Horizontal multistage end suction pumps are an essential component in many industries, including water treatment, power generation, chemical processing, and oil & gas. In today’s blog post, we’ll take an in-depth look at the advantages of horizontal multistage end suction pumps, exploring their design, operational benefits, energy efficiency, ease of maintenance, and much more. Whether you’re an engineer seeking detailed technical insights or a facility manager evaluating your options, this comprehensive guide is designed to offer valuable insights in an engaging and relatable manner.
Introduction
The modern industrial landscape demands reliability, efficiency, and versatility from every piece of equipment. Horizontal multistage end suction pumps have emerged as a reliable solution for numerous applications where high pressure and low flow conditions are common. Their robust design, optimized performance, and flexible installation options make them indispensable. In this article, we’ll dive into the top advantages of horizontal multistage end suction pumps, discuss their operational features, and highlight why they are a preferred choice in many industrial applications.
Our discussion will cover:
- Design and Engineering Excellence: How these pumps are designed for high efficiency.
- Performance and Efficiency: The technical aspects that contribute to their operational excellence.
- Ease of Maintenance and Longevity: What makes them reliable and cost-effective in the long run.
- Installation and Operational Flexibility: Benefits that enhance user experience.
- Real-World Applications and Case Studies: Examples that illustrate their advantages in practice.
- Future Trends and Innovations: How ongoing advancements continue to improve pump performance.
Let’s start by exploring the fundamentals of horizontal multistage end suction pumps and what sets them apart.
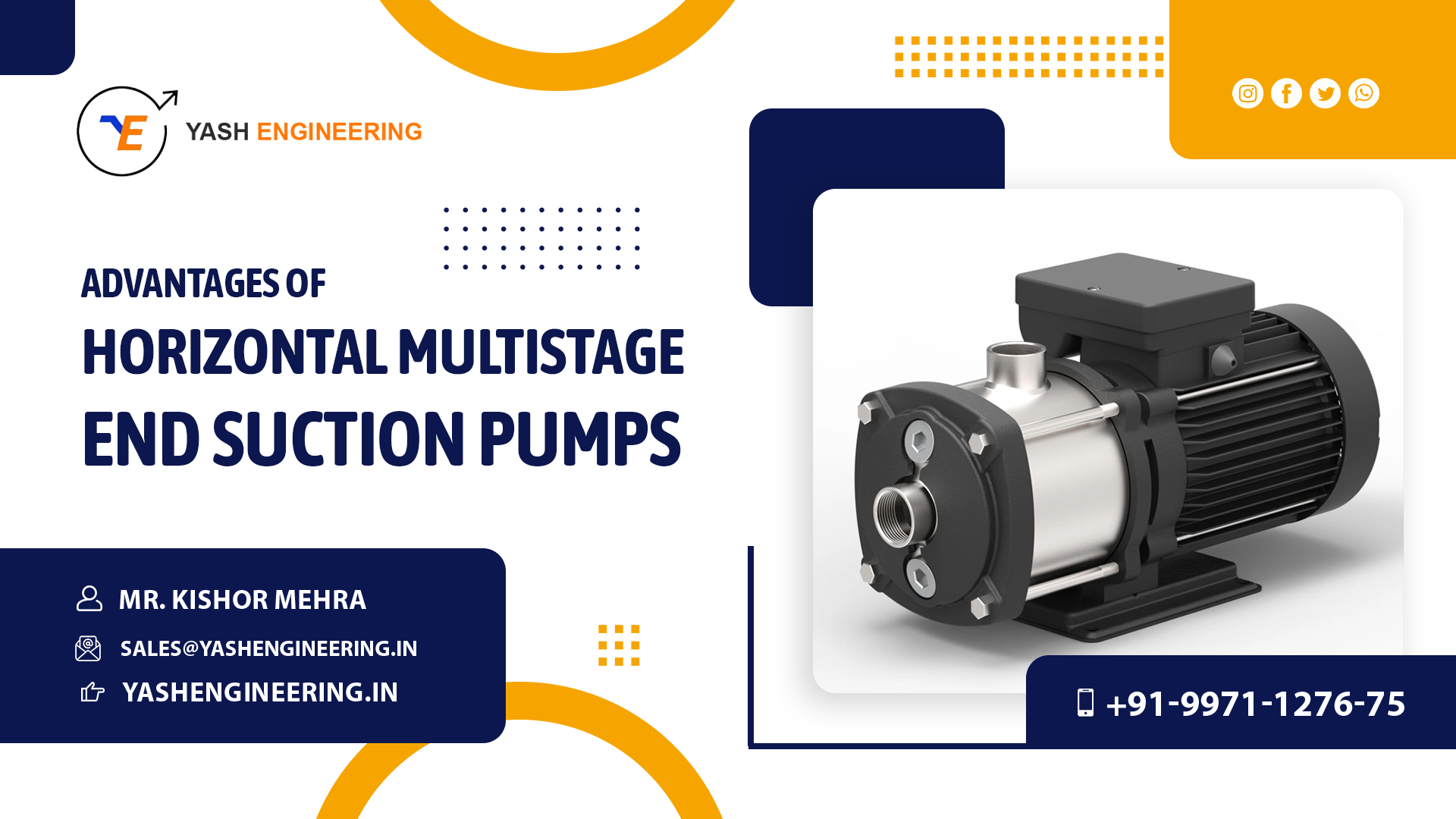
Understanding Horizontal Multistage End Suction Pumps
What Are They?
Horizontal multistage end suction pumps are centrifugal pumps that incorporate multiple impeller stages arranged in a horizontal configuration. Unlike single-stage pumps, these pumps use several impellers to generate higher pressures while maintaining a relatively compact size. They are designed to handle applications requiring high heads and moderate flow rates.
Key Design Elements
- Multiple Stages: Each impeller stage contributes incrementally to the overall head (pressure) output. This multi-stage design is crucial for achieving high pressures without compromising efficiency.
- Horizontal Layout: The horizontal design allows for easy alignment and installation. It also facilitates better maintenance access and simpler integration into existing systems.
- End Suction Configuration: With the suction inlet positioned at one end of the pump casing, the design promotes a streamlined flow, reduces turbulence, and improves overall pump efficiency.
- Robust Materials: These pumps are built using high-quality materials to withstand harsh operating conditions, corrosive environments, and high pressures, ensuring long service life.
How They Operate
The operation of horizontal multistage end suction pumps relies on the centrifugal force generated by the impellers. As fluid enters the pump, it is accelerated radially outward through each impeller stage. With each stage, the fluid’s pressure increases before it exits the pump at the discharge side. This method of operation ensures that the fluid is moved efficiently even at high pressure differentials.
Advantages of Horizontal Multistage End Suction Pumps
When evaluating pumping solutions, understanding the advantages of horizontal multistage end suction pumps is paramount. Below, we delve into several key benefits that make these pumps a superior choice for many industrial applications.
1. High Efficiency and Superior Performance
One of the primary advantages of horizontal multistage end suction pumps is their high operational efficiency. The multistage design allows for the creation of significant pressure increases while minimizing energy losses. Key performance benefits include:
- Enhanced Pressure Generation: Each impeller stage works in tandem to boost the fluid’s pressure. This makes these pumps ideal for high head applications, such as boiler feedwater and reverse osmosis systems.
- Energy Savings: Due to their high efficiency, these pumps can reduce energy consumption significantly compared to single-stage or less sophisticated pump designs. The reduced energy usage not only saves on operating costs but also contributes to sustainability efforts.
- Stable Operation: The design helps maintain a consistent flow, even under varying load conditions. This stability is particularly beneficial in processes where precise control over fluid dynamics is crucial.
The inherent energy efficiency of horizontal multistage end suction pumps means that industries can enjoy lower operational costs over the life cycle of the pump, providing a compelling return on investment.
2. Compact and Space-Saving Design
Space is often at a premium in industrial settings, and the compact design of these pumps is a significant advantage. The horizontal layout ensures that the pump occupies less floor space compared to vertical or more complex configurations. Benefits include:
- Simplified Installation: The horizontal configuration simplifies installation procedures, reducing the time and labor required for setup.
- Ease of Integration: Their compact nature allows for easier retrofitting into existing systems without major structural modifications.
- Improved Accessibility: The design facilitates easier access for routine inspections, maintenance, and repairs, minimizing downtime and ensuring smooth operations.
3. Enhanced Reliability and Durability
Reliability is a non-negotiable factor in industrial operations. Horizontal multistage end suction pumps are engineered for durability under demanding conditions. Here are some key points highlighting their reliability:
- Robust Construction: Built to withstand high pressure, temperature fluctuations, and corrosive fluids, these pumps are designed for longevity.
- Reduced Wear and Tear: The efficient flow dynamics and balanced design reduce mechanical stress on components, leading to lower wear rates and fewer maintenance issues.
- Consistent Performance: Even under continuous operation, these pumps deliver stable performance, ensuring that process flows remain uninterrupted.
Industries that demand uninterrupted service and minimal maintenance downtime will appreciate the long-lasting nature of horizontal multistage end suction pumps.
4. Ease of Maintenance
Maintenance considerations are central to operational cost and efficiency. The design of these pumps inherently reduces maintenance complexity through:
- Accessible Components: With a horizontal layout, critical components are more accessible, making routine checks and part replacements straightforward.
- Simplified Disassembly: Many models are designed with ease-of-disassembly in mind, allowing technicians to quickly access and replace worn parts.
- Minimized Downtime: Faster maintenance translates to reduced downtime, ensuring that production processes are not significantly disrupted during service intervals.
Routine maintenance is vital for long-term reliability, and the ease with which these pumps can be serviced adds to their overall appeal.
5. Versatile Applications
Another significant advantage of horizontal multistage end suction pumps is their versatility. They are designed to handle a wide range of fluids and process conditions, which makes them suitable for diverse applications such as:
- Water Treatment Plants: Providing reliable feedwater for boilers and other high-pressure systems.
- Chemical Processing: Handling corrosive and abrasive fluids while maintaining consistent performance.
- Power Generation: Serving as a critical component in cooling and process water systems in power plants.
- Oil and Gas: Managing high-pressure fluids in both upstream and downstream operations.
This versatility means that industries across the board can benefit from the specialized design of horizontal multistage end suction pumps.
6. Energy Efficiency and Cost Savings
In today’s environmentally conscious world, energy efficiency is more critical than ever. Horizontal multistage end suction pumps offer notable energy savings due to:
- Optimized Hydraulic Design: The multiple stages ensure that energy is effectively converted into pressure, reducing energy losses.
- Lower Operational Costs: Energy-efficient pumps contribute to significant reductions in energy bills over time.
- Sustainability Benefits: Reduced energy consumption aligns with environmental regulations and sustainability goals, making these pumps a smart choice for eco-conscious operations.
Lower energy consumption not only improves the bottom line but also supports broader sustainability initiatives that are becoming increasingly important in industrial operations.
7. Improved Process Control
For many industrial applications, precise process control is essential. Horizontal multistage end suction pumps offer:
- Stable Flow Rates: Their design ensures a consistent flow, even during fluctuations in system demand.
- Adjustable Performance: Many models feature variable speed drives or other control mechanisms that allow operators to adjust the pump performance to match process requirements.
- Integrated Monitoring: Modern pumps often come with integrated sensors and control systems that provide real-time data, helping operators optimize performance and detect potential issues before they escalate.
Improved process control translates directly to enhanced operational efficiency and better product quality, which is crucial in high-stakes industrial environments.
8. Lower Noise Levels and Vibrations
Noise and vibrations can be a significant concern in industrial settings, both for worker comfort and equipment longevity. Horizontal multistage end suction pumps are engineered to reduce these issues through:
- Balanced Design: The symmetrical arrangement of impellers helps in balancing forces within the pump, leading to reduced vibrations.
- Advanced Materials: The use of high-quality materials dampens the transmission of noise and vibrations.
- Operational Smoothness: Enhanced flow dynamics minimize turbulence, contributing to quieter operation and a more stable system.
Lower noise and vibration levels contribute to a safer and more comfortable working environment, which is an often overlooked but important advantage of these pumps.
9. Cost-Effective Over the Long Term
While the initial investment in horizontal multistage end suction pumps may be higher than simpler pump designs, the long-term cost benefits are significant:
- Reduced Maintenance Costs: The ease of maintenance and robust construction mean fewer unexpected breakdowns and lower repair costs.
- Energy Savings: The high efficiency translates to substantial energy savings over the pump’s lifetime.
- Longer Service Life: With proper care, these pumps can provide reliable service for many years, offsetting the initial capital expenditure.
When evaluating total cost of ownership, the long-term savings associated with horizontal multistage end suction pumps make them a cost-effective choice for many industrial applications.
10. Customizable to Specific Needs
One of the standout advantages of horizontal multistage end suction pumps is their flexibility in design, which allows for customization to meet specific operational requirements. Manufacturers often offer options to tailor the pump to a client’s particular application, including:
- Variable Stage Configurations: Depending on the pressure and flow requirements, pumps can be designed with a specific number of stages.
- Material Selection: Different materials can be chosen to resist corrosion, abrasion, or other environmental challenges.
- Performance Tuning: Advanced control options can be integrated, allowing the pump to be fine-tuned for optimal performance under varying conditions.
Customization ensures that each pump installation is optimized for its specific application, providing a tailored solution that maximizes performance and efficiency.
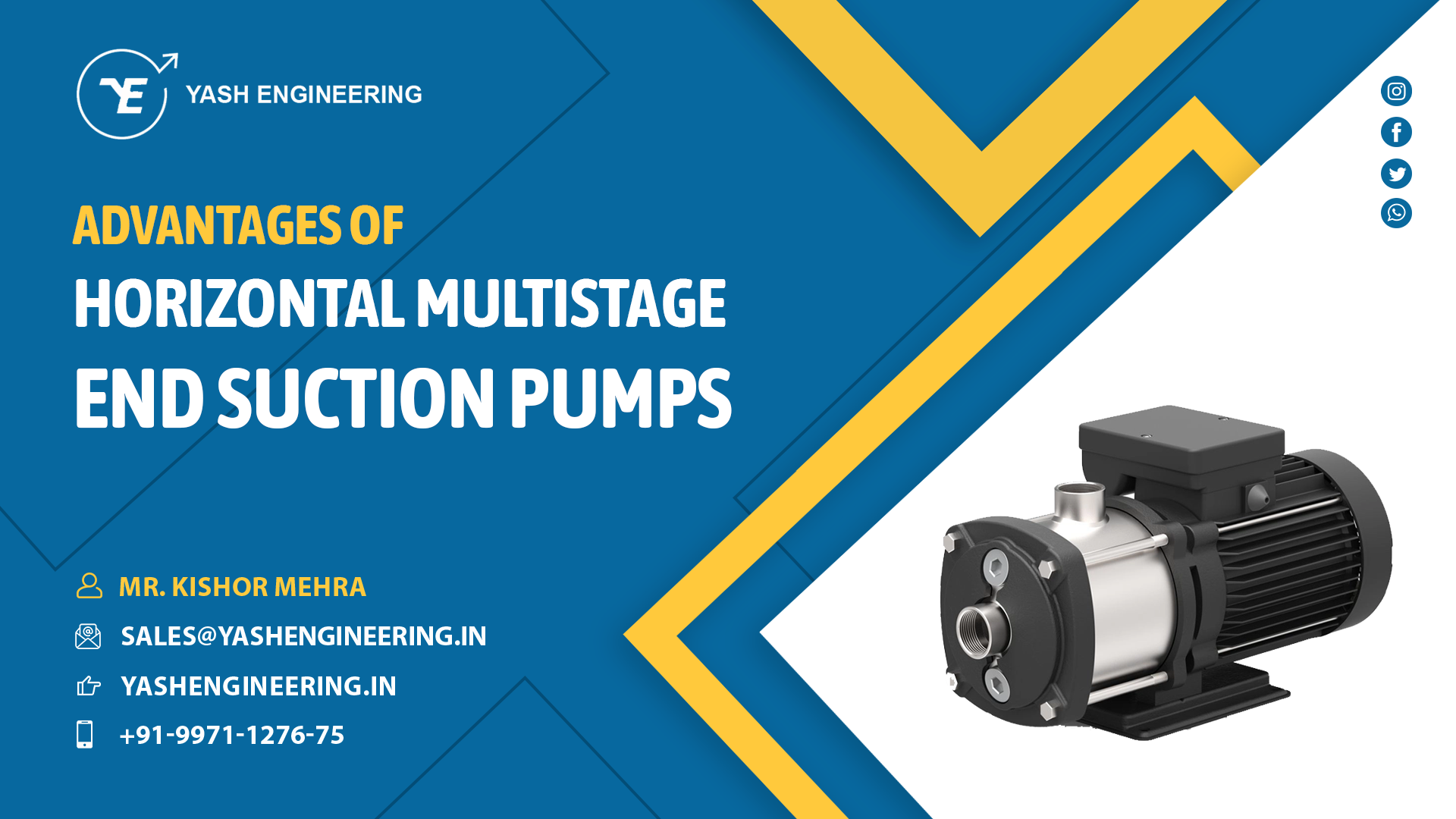
Technical Insights: How Horizontal Multistage End Suction Pumps Achieve Superior Performance
Fluid Dynamics and Flow Optimization
At the heart of the advantages of horizontal multistage end suction pumps lies a deep understanding of fluid dynamics. The multi-stage design takes full advantage of centrifugal force to create a smooth, continuous flow that maximizes energy conversion. Here’s how it works:
- Centrifugal Acceleration: As the fluid enters the pump, the impellers accelerate it outward. This acceleration increases the kinetic energy, which is then converted into pressure energy.
- Sequential Energy Addition: Each impeller stage adds a specific increment of pressure. By the time the fluid exits the final stage, the cumulative pressure is significantly higher than what a single-stage pump could achieve.
- Flow Stabilization: The design minimizes turbulence and recirculation within the pump casing, leading to a stable and predictable flow. This is especially important in applications that require precise control over the process conditions.
The technical excellence in the pump’s design results in an operational efficiency that is unmatched in many applications, making it an ideal solution for industries that rely on precision and performance.
Advanced Manufacturing Techniques
Modern manufacturing techniques play a crucial role in the superior performance of horizontal multistage end suction pumps. Innovations in computer-aided design (CAD) and advanced machining allow manufacturers to produce components with tight tolerances, ensuring that each pump operates at peak efficiency. Benefits include:
- Precision Engineering: Tight tolerances reduce energy losses and enhance the pump’s overall efficiency.
- Quality Control: Rigorous quality control processes ensure that each pump meets stringent performance standards, reducing the likelihood of failures.
- Innovation: Ongoing research and development continue to refine pump designs, incorporating new materials and techniques to further enhance performance and durability.
These technical insights underscore why horizontal multistage end suction pumps are at the forefront of industrial pump technology.
Real-World Applications: Case Studies and Industry Examples
To truly appreciate the advantages of horizontal multistage end suction pumps, it is helpful to examine how they perform in real-world scenarios. Below are some case studies and examples drawn from various industries.
Case Study 1: Water Treatment Plant
Background:
A municipal water treatment plant required a reliable solution to handle high-pressure feedwater for its boiler system. The existing single-stage pumps were struggling to maintain the necessary pressure, leading to inefficiencies and increased maintenance costs.
Solution:
The plant management opted to install horizontal multistage end suction pumps. The multi-stage design allowed the facility to achieve the desired pressure with greater energy efficiency. Installation was straightforward due to the compact, horizontal layout, and routine maintenance became simpler and more predictable.
Results:
- Improved Efficiency: The new pumps provided stable performance, reducing energy consumption and operational costs.
- Reduced Downtime: Easier maintenance procedures translated to fewer service interruptions.
- Extended Service Life: The robust design ensured that the pumps withstood the rigorous demands of continuous operation.
Case Study 2: Chemical Processing Facility
Background:
In a chemical processing facility, handling corrosive and abrasive fluids was a significant challenge. The pumps used previously experienced frequent wear, leading to costly repairs and unscheduled downtime.
Solution:
The facility chose horizontal multistage end suction pumps designed with corrosion-resistant materials. The pumps’ robust construction and customizable design allowed them to handle aggressive chemicals without compromising performance.
Results:
- Enhanced Durability: The pumps demonstrated exceptional resistance to wear, reducing the frequency of maintenance interventions.
- Energy Efficiency: Despite the harsh operating environment, the pumps maintained high energy efficiency, contributing to overall cost savings.
- Process Control: The stable flow and precise control offered by the pumps ensured consistent quality in the chemical processing operations.
Case Study 3: Power Generation Plant
Background:
A power generation plant needed to upgrade its cooling water system to ensure reliable operation during peak loads. The previous pumping system was not optimized for the high-pressure requirements, leading to inefficiencies.
Solution:
By installing horizontal multistage end suction pumps, the plant was able to achieve the necessary head while maintaining energy efficiency. The pumps were integrated into the existing system with minimal modifications, thanks to their compact design.
Results:
- Reliable Performance: The new pumps provided consistent pressure and flow, critical for the plant’s cooling system.
- Energy Savings: Lower energy consumption contributed to reduced operational costs.
- Ease of Integration: The horizontal layout facilitated seamless integration with the plant’s existing infrastructure, minimizing installation downtime.
Future Trends and Innovations
The world of pump technology is continuously evolving, and horizontal multistage end suction pumps are no exception. Several trends and innovations are shaping the future of these pumps, promising even greater performance, efficiency, and adaptability.
Integration of Smart Technologies
One of the most exciting advancements in pump technology is the integration of smart technologies and digital monitoring systems. By incorporating sensors, IoT (Internet of Things) devices, and real-time monitoring systems, manufacturers are enabling operators to:
- Monitor Performance: Gain real-time insights into flow rates, pressures, and energy consumption.
- Predict Maintenance Needs: Use predictive analytics to anticipate potential issues before they cause failures.
- Optimize Operations: Adjust pump performance dynamically to match process demands, further enhancing energy efficiency.
The digital transformation in pump technology is expected to drive further improvements in reliability and operational efficiency.
Enhanced Materials and Coatings
Advancements in material science continue to impact the design of horizontal multistage end suction pumps. New materials and protective coatings are being developed to extend the lifespan of pumps operating in aggressive environments. These innovations include:
- Corrosion-Resistant Alloys: To better handle chemicals and saltwater environments.
- Wear-Resistant Coatings: Which minimize the impact of abrasive fluids on pump components.
- Lightweight Composites: That reduce overall pump weight while maintaining structural integrity.
These material innovations not only improve the durability of the pumps but also contribute to lower maintenance costs and extended service life.
Energy Recovery and Sustainability
Energy efficiency remains a top priority for industrial equipment. Future developments in horizontal multistage end suction pumps may include technologies aimed at energy recovery and further reducing environmental impact. Potential advancements include:
- Integrated Energy Recovery Systems: That capture and reuse energy from the pump operation.
- Eco-Friendly Designs: Focusing on reducing the carbon footprint and overall environmental impact of pump systems.
- Optimization Algorithms: Using advanced software to dynamically adjust pump parameters for maximum efficiency.
Such developments are likely to make these pumps even more attractive for industries that prioritize sustainability alongside performance.
Customization and Modular Designs
Manufacturers are increasingly offering modular pump designs that allow for greater customization to meet specific industrial needs. Modular designs facilitate:
- Flexible Configurations: Allowing users to easily adapt the pump to various operating conditions.
- Scalability: Enabling the pump system to grow with the demands of the facility.
- Cost-Effective Upgrades: Providing a straightforward pathway for future enhancements without the need for complete system overhauls.
The ability to customize and adapt pumps to meet evolving requirements will continue to be a key selling point for horizontal multistage end suction pumps.
Practical Tips for Choosing the Right Pump
Selecting the right pump for your application can be a daunting task. To help guide your decision-making process, consider the following practical tips:
1. Evaluate Your Specific Needs
Before choosing a pump, assess your process requirements:
- Flow Rate: Determine the required flow rate for your application.
- Pressure Requirements: Understand the head (pressure) needed to meet your process demands.
- Fluid Characteristics: Consider the properties of the fluid, such as viscosity, temperature, and corrosiveness.
2. Consult with Experts
Working with experienced engineers and pump specialists can help you:
- Identify the Best Configuration: Based on your operational requirements.
- Customize the Design: Ensure that the pump is tailored to your specific application.
- Ensure a Smooth Installation: With expert guidance, integration into your existing system can be seamless.
3. Consider Long-Term Costs
While upfront costs are important, long-term operational and maintenance costs should be factored into your decision:
- Energy Consumption: A high-efficiency pump can reduce operating costs.
- Maintenance Needs: Pumps that are easier to service can reduce downtime and repair expenses.
- Service Life: Investing in a durable, long-lasting pump often results in better overall cost efficiency.
4. Review Case Studies and Testimonials
Looking at real-world examples and customer testimonials can provide insight into the performance and reliability of a pump in similar applications. This can help you:
- Gauge Reliability: Understand how the pump has performed in environments similar to yours.
- Identify Potential Challenges: Learn from others’ experiences regarding maintenance and operational issues.
- Make an Informed Decision: Build confidence in your choice based on proven performance data.
Integration and Installation: Getting the Most Out of Your Pump
Proper integration and installation of horizontal multistage end suction pumps are critical to maximizing their advantages. Here are some best practices to ensure a smooth installation process:
Pre-Installation Planning
- Site Assessment: Conduct a thorough evaluation of the installation site to determine space requirements, environmental conditions, and existing infrastructure.
- Custom Design Considerations: Work closely with the manufacturer to customize the pump’s design to match your operational needs.
- Project Scheduling: Plan the installation during a period that minimizes disruption to your operations, and allocate sufficient time for testing and commissioning.
Installation Best Practices
- Alignment and Mounting: Ensure that the pump is properly aligned and securely mounted to minimize vibrations and mechanical stress.
- Piping and Connections: Use high-quality piping and connections to reduce the risk of leaks and ensure smooth fluid flow.
- Electrical and Control Systems: Integrate the pump with your existing control systems, and consider incorporating advanced monitoring devices for real-time performance tracking.
Post-Installation Procedures
- Initial Testing: Conduct a thorough testing phase to verify that the pump meets all performance parameters before full-scale operation.
- Operator Training: Train your staff on the operational characteristics of the pump, including routine maintenance and troubleshooting procedures.
- Ongoing Monitoring: Implement a regular monitoring schedule to detect any performance deviations early, allowing for proactive maintenance.
The Human Side of Industrial Pumping
While the technical aspects of horizontal multistage end suction pumps are fascinating, it’s important to remember the human element behind these systems. For engineers, facility managers, and technicians, these pumps represent not only an investment in technology but also a commitment to safety, reliability, and efficiency in the workplace.
Building Confidence Through Reliability
When industrial processes depend on the continuous flow of fluids—be it for cooling, processing, or power generation—the reliability of the pump is paramount. A pump that fails unexpectedly can lead to costly downtime and even safety hazards. The dependable nature of horizontal multistage end suction pumps gives peace of mind to those who rely on them every day.
Enhancing Worker Safety and Comfort
The design advantages, such as reduced noise and vibrations, translate into a better working environment. A quieter, more stable pump means that maintenance crews and operators experience less stress and physical strain. Over time, this contributes to improved job satisfaction and a stronger sense of pride in the work environment.
Empowering Through Innovation
For many professionals in the industry, staying abreast of technological advancements is a source of motivation and pride. Knowing that they are working with state-of-the-art equipment that continuously evolves to meet new challenges fosters a culture of innovation and continuous improvement. Whether it’s integrating smart monitoring systems or adopting new materials, the evolution of horizontal multistage end suction pumps reflects a broader trend towards smarter, more sustainable industrial operations.
In-Depth Technical Comparisons
To fully appreciate the advantages of horizontal multistage end suction pumps, it’s beneficial to compare them with alternative pump types. Here, we outline some key differences:
Single-Stage vs. Multistage Pumps
-
Pressure Generation:
- Single-Stage Pumps: Typically used for low to medium pressure applications.
- Multistage Pumps: Capable of achieving much higher pressures due to the cumulative effect of multiple impeller stages.
-
Efficiency:
- Single-Stage Pumps: Generally less energy-efficient when high pressure is required.
- Multistage Pumps: Optimized to convert energy more effectively into pressure, reducing energy losses.
-
Application Scope:
- Single-Stage Pumps: Best suited for applications with moderate flow requirements.
- Multistage Pumps: Ideal for high head applications like boiler feedwater, reverse osmosis, and high-pressure cleaning systems.
Vertical vs. Horizontal Pump Configurations
-
Installation and Accessibility:
- Vertical Pumps: Often require more complex piping and alignment considerations.
- Horizontal Pumps: Offer easier installation, better accessibility for maintenance, and a more compact footprint.
-
Vibration and Noise:
- Vertical Pumps: May experience higher vibrations and noise levels depending on the design.
- Horizontal Pumps: Typically designed to minimize vibrations, contributing to a quieter operational environment.
These comparisons highlight why horizontal multistage end suction pumps are often the preferred choice for applications where high pressure, efficiency, and ease of maintenance are key factors.
Environmental Considerations and Sustainability
In today’s industrial environment, sustainability is no longer just a buzzword—it’s a necessity. Horizontal multistage end suction pumps contribute positively to environmental goals in several ways:
Energy Efficiency and Carbon Footprint
As discussed, the high efficiency of these pumps directly translates into lower energy consumption. Reduced energy usage not only decreases operating costs but also lowers the overall carbon footprint of industrial operations. For companies striving to meet environmental regulations and corporate sustainability goals, this is a major advantage.
Resource Optimization
Efficient pumps optimize the use of water and other fluids, reducing waste and improving process sustainability. This is particularly relevant in water treatment and chemical processing industries, where resource optimization can lead to significant cost savings and environmental benefits.
Reduced Maintenance and Waste
A pump that requires less frequent maintenance generates less waste from spare parts and reduces the need for chemical cleaning agents. Over the long term, this contributes to a more sustainable operation with fewer environmental impacts.
Lessons Learned from Industry Veterans
Throughout the years, many professionals have shared their experiences with horizontal multistage end suction pumps. Here are some insights from industry veterans that underline the advantages of these pumps:
Reliability in Harsh Conditions
Veteran engineers consistently praise the ability of these pumps to operate reliably in harsh environments. Whether in chemical plants or coastal water treatment facilities, the pumps’ durability and performance have been noted as key factors in maintaining continuous operations.
The Value of Ease of Maintenance
Maintenance teams appreciate the straightforward design of horizontal multistage end suction pumps. Quick access to key components, coupled with clear diagnostic indicators, reduces downtime and allows for proactive service. This ease of maintenance not only cuts costs but also extends the pump’s operational lifespan.
Energy and Cost Savings
Over the years, many companies have recorded significant energy savings and lower overall operational costs after switching to horizontal multistage end suction pumps. These savings are often highlighted as one of the most compelling reasons to invest in such technology.
Frequently Asked Questions
To wrap up our exploration of the advantages of horizontal multistage end suction pumps, here are some frequently asked questions that address common concerns and provide additional clarity:
Q1: What makes horizontal multistage end suction pumps different from other pump types?
Horizontal multistage end suction pumps are distinguished by their multiple impeller stages, horizontal design, and ease of maintenance. This combination allows them to generate high pressure efficiently, making them ideal for high head applications and industrial processes requiring reliable performance.
Q2: How do these pumps contribute to energy efficiency?
Their multistage design ensures that energy is effectively converted into pressure, reducing energy losses and lowering operational costs. Additionally, modern models often incorporate smart controls and variable speed drives to optimize performance further.
Q3: Are horizontal multistage end suction pumps difficult to install?
Not at all. Their horizontal configuration is designed to simplify installation, minimize space requirements, and facilitate easy integration with existing systems. This makes them an attractive option for both new installations and retrofits.
Q4: What kind of maintenance do these pumps require?
Maintenance is generally straightforward due to the accessible layout of the components. Regular inspections, timely replacement of wear parts, and proper alignment are typically sufficient to ensure long-term reliability and performance.
Q5: In what industries are these pumps most commonly used?
They are widely used in water treatment, chemical processing, power generation, and oil & gas industries, among others. Their versatility and robust design make them suitable for any application that requires high-pressure fluid transport.
Conclusion
Horizontal multistage end suction pumps represent a convergence of innovative engineering, robust design, and practical efficiency. From their ability to generate high pressures in a compact form factor to their impressive energy efficiency and ease of maintenance, the advantages of horizontal multistage end suction pumps are clear.
In industrial applications where reliability, cost savings, and environmental considerations are paramount, these pumps stand out as a highly effective solution. Their adaptability to various operational conditions, coupled with ongoing advancements in smart technologies and materials, ensures that they will continue to be a cornerstone of modern industrial fluid handling.
For engineers, plant managers, and decision-makers alike, investing in horizontal multistage end suction pumps is not just a technical upgrade—it’s a strategic move towards a more efficient, sustainable, and reliable future.
Final Thoughts
The evolution of pump technology is a testament to human ingenuity and the relentless pursuit of excellence in industrial processes. Horizontal multistage end suction pumps embody these ideals by delivering exceptional performance, energy savings, and durability. Whether you are upgrading an existing system or designing a new facility, understanding and leveraging the unique advantages of these pumps can provide significant operational benefits and long-term cost savings.
We hope this blog post has offered valuable insights into the top advantages of horizontal multistage end suction pumps. Their blend of efficiency, compact design, and durability positions them as an ideal solution for a wide array of industrial applications. As industries continue to evolve and embrace sustainability, the role of these pumps will undoubtedly expand, driving innovation and operational excellence for years to come.
By focusing on the benefits such as enhanced energy efficiency, ease of maintenance, and improved process control, you can make an informed decision that not only meets your operational requirements but also contributes to a more sustainable industrial future.
Thank you for taking the time to explore this comprehensive guide with us. If you have any questions or would like to share your own experiences with horizontal multistage end suction pumps, please feel free to comment below. Your feedback and insights help build a more knowledgeable and connected community.